
Process
OxFA has developed an innovative, catalytic process for the efficient utilisation of biomass and the production of bio-based formic acid (bio-FA) and derivative products. The sustainable chemicals can be produced with high yields and 100 % biogenic carbon content. In addition to the very mild reaction conditions of < 6 bar, <140 °C and water as the only environmentally friendly solvent, our process has several advantages. The technical process can be subdivided in three parts, the pretreatment of biomass, the oxidation process and the isolation of main product: bio formic acid.
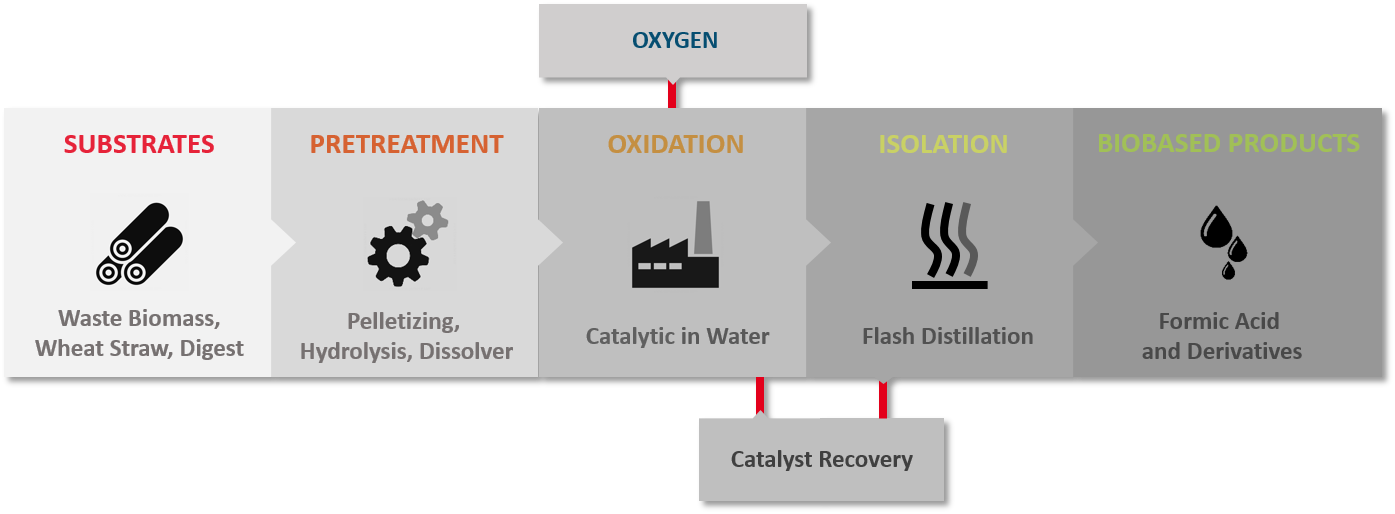
- wide range of organic materials and residues
- wet and lignified biomass
- more than 30 million tons of unused technical biomass only in Germany
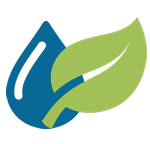
wet and lignified biomass
technical biomass potential in Germany
- optional pretreatment of solid biomass
- low substrate requirements of OxFA process allow for conventional pulping technologies
- tailor made pretreatment with technology partners

mechanical

acidic hydrolysis

enzymatic
- catalytic oxidation with oxygen from air
- mild reaction conditions (pressure and temperature)
- patented catalyst family from own productions
T < 140 °C
low temperatures
p < 6 bar
low pressure
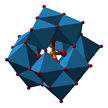
patented catalyst
- simple thermal isolation for lower formic acid concentrations > 50 %wt
- high formic acid concentration > 95 %wt by patented extraction process
- no NOx or SO2 in exhaust

thermal
50-75 %wt. formic acid

extractive
> 95 %wt. formic acid
Competitive Advantage

efficient – high throughput
short residence times due to noble metal free catalyst, no additives, mild reaction conditions, low energy consumption

selective – low amount of residues
FA and CO2 as main products, no wide product distribution, little isolation and downstream requirements

practical – low pressure and temperature
low equipment costs, low operating costs, smaller installation, safer handling

flexible – wet and lignified biomass
water soluble and non-soluble biomass, wet and lignified biomass, huge potential of technically usable biomass

decentralized – short transportation distances
ubiquitous biomass and biogenic residues, smaller plants for decentralized production, modular and standardized production

bio-based – exclusive upside potential
formic acid as bio-based platform chemical, a variety of additional products from syngas, deicing agents to synthetic fuels and additives
From simple sugars to complex biomass many biogenic feedstocks are suitable
A special feature of the OxFA process is that the biomass used can be both hydrous and lignified. Due to the low demands of the process on biogenic feedstock, a broad range of biomass can be implemented in the process. Whether algae, bagasse, wood, corn silage, wheat straw or sugar beets: Many renewable raw materials can be converted into bio-based formic acid. Even residues from the food industry such as molasses, vinasses, pressed pulp, spent grain and pomace are also an excellent starting material for biogenic formic acid. Formic acid can be obtained sustainably even from waste such as fermentation residues or biological sewage or sewage sludge. Sugar and starch containing biomass exhibits extraordinary high yields in formic acid.
Depending on the substrate, up to one kilogram bio-based formic acid per kilogram dry matter can be produced.
IP and Patents
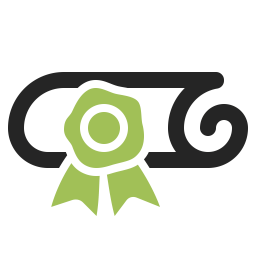
OxFA technology is patented on different levels of the process. We have several patents directly applied by OxFA, others were purchased and there is technical know-how not being disclosed. Our portfolio contains the catalyst itself, reactor design and process design as well as the downstream process to formic acid and it´s derivatives.
Research and Development
The OxFA process is based on intensive fundamental research in the field of catalytic oxygenation of biomass within the Chair of Chemical Reaction Engineering of the Friedrich-Alexander university (FAU) Erlangen-Nuremberg.
The OxFA GmbH commercializes the proprietary technology and optimizes the necessary catalysts and reaction technology. In further research projects together with the FAU and the Ostbayerischen Technischen Hochschule Amberg-Weiden new fields of application and downstream processes regarding also the field of bio-based are investigated. Here you can find a selection of published work:
Energy & Environmental Science (2012)
Selective oxidation of complex, water-insoluble biomass to formic acid using additives as reaction accelerators
J. Albert et al.
Energy Environ. Sci., 2012,5, 7956-7962
Energy & Environmental Science (2015)
Biomass oxidation to formic acid in aqueous media using polyoxometalate catalysts – boosting FA selectivity by in-situ extraction
J. Reichert et al.
Energy Environ. Sci., 2015,8, 2985-2990
Green Chemistry (2015)
Expanding the scope of biogenic substrates for the selective production of formic acid from water-insoluble and wet waste biomass
J. Albert, P. Wasserscheid
Green Chem., 2015,17, 5164-5171
ACS Sustainable Chemistry & Engineering (2016)
Formic Acid-Based Fischer–Tropsch Synthesis for Green Fuel Production from Wet Waste Biomass and Renewable Excess Energy
J. Albert et al.
ACS Sustainable Chem. Eng. 4, 9, 5078-5086
ACS Sustainable Chemistry & Engineering (2017)
Detailed kinetic investigations on the selective oxidation of biomass to formic acid (OxFA Process) using model substrates and real biomass
J. Reichert, J. Albert
ACS Sustainable Chem. Eng. 5, 8, 7383-7392
ACS OMEGA 2 (2017)
Measuring and Predicting the Extraction Behavior of Biogenic Formic Acid in Biphasic Aqueous/Organic Reaction Mixtures
H. Veith et al.
ACS Omega 2, 12, 8982-8989
Energy Technology (2018)
Biogenic formic acid as a green hydrogen carrier
P. Preuster, J. Albert
Energy Technol., 2018,6, 501 –509
Green Chemistry (2020)
Glucose oxidation to formic acid and methyl formate in perfect selectivity
S. Maerten, C. Kumpidet, D. Voß, A. Bukowski, P. Wasserscheid and J. Albert
Green chem., 2020, 22, 4311-4320
Biomass Conversion and Biorefinery (2023)
Valorization of secondary feedstocks from the agroindustry by selective catalytic oxidation to formic and acetic acid using the OxFA process
S. Ponce, S. Wesinger, D. Ona, D. Almeida Streitwieser & J. Albert
Biomass Conv. Bioref. 2023, 13, 7199–7206
International Journal of Hydrogen Energy (2024)
Hydrogen production from wet biomass via a formic acid route under mild conditions
F. Kroll, M. Schörner, M. Schmidt, F.T.U. Kohler, J. Albert, P. Schühle
International Journal of Hydrogen Energy, 2024, 62, 959–968